Garis Injeksi Kimia Downhole-Mengapa Mereka Gagal?Pengalaman, Tantangan dan Penerapan Metode Tes Baru
Hak Cipta 2012, Masyarakat Insinyur Perminyakan
Abstrak
Statoil mengoperasikan beberapa bidang di mana downhole continuous injection of scale inhibitor diterapkan.Tujuannya adalah untuk melindungi tubing atas dan katup pengaman dari (Ba/Sr) SO4orCaCO;skala, dalam kasus di mana skala pemerasan mungkin sulit dan mahal untuk dilakukan secara teratur, misalnya pengikatan lapangan bawah laut.
Injeksi downhole penghambat kerak secara terus-menerus adalah solusi yang tepat secara teknis untuk melindungi tabung atas dan katup pengaman di sumur yang memiliki potensi kerak di atas pengemas produksi;terutama pada sumur yang tidak perlu dipencet secara rutin karena potensi scaling di dekat lubang sumur.
Merancang, mengoperasikan, dan memelihara jalur injeksi bahan kimia menuntut fokus ekstra pada pemilihan bahan, kualifikasi bahan kimia, dan pemantauan.Tekanan, suhu, rezim aliran, dan geometri sistem dapat menimbulkan tantangan pada pengoperasian yang aman.Tantangan telah diidentifikasi pada jalur injeksi sepanjang beberapa kilometer dari fasilitas produksi ke templat bawah laut dan pada katup injeksi di dalam sumur.
Pengalaman lapangan yang menunjukkan kompleksitas sistem injeksi kontinu downhole mengenai masalah presipitasi dan korosi dibahas.Studi laboratorium dan penerapan metode baru untuk kualifikasi kimia diwakili.Kebutuhan untuk tindakan multidisiplin ditangani.
Perkenalan
Statoil mengoperasikan beberapa bidang di mana injeksi bahan kimia terus-menerus downhole telah diterapkan.Ini terutama melibatkan injeksi penghambat skala (SI) di mana tujuannya adalah untuk melindungi tabung atas dan katup pengaman lubang bawah (DHSV) dari (Ba/Sr) SO4orCaCO;skala.Dalam beberapa kasus pemecah emulsi disuntikkan ke bawah lubang untuk memulai proses pemisahan sedalam mungkin di dalam sumur pada suhu yang relatif tinggi.
Injeksi terus-menerus downhole penghambat kerak adalah solusi yang tepat secara teknis untuk melindungi bagian atas sumur yang memiliki potensi kerak di atas pengemas produksi.Injeksi kontinu mungkin direkomendasikan terutama pada sumur yang tidak perlu diperas karena potensi penskalaan yang rendah di dekat lubang sumur;atau dalam kasus di mana scale squeezing mungkin sulit dan mahal untuk dilakukan secara rutin, misalnya pengikatan lapangan bawah laut.
Statoil telah memperluas pengalaman injeksi bahan kimia terus menerus ke sistem topside dan template bawah laut, tetapi tantangan barunya adalah membawa titik injeksi lebih jauh ke dalam sumur.Merancang, mengoperasikan, dan memelihara jalur injeksi kimia menuntut fokus ekstra pada beberapa topik;seperti pemilihan bahan, kualifikasi bahan kimia dan pemantauan.Tekanan, suhu, rezim aliran, dan geometri sistem dapat menimbulkan tantangan pada pengoperasian yang aman.Tantangan dalam jalur injeksi panjang (beberapa kilometer) dari fasilitas produksi ke templat bawah laut dan ke katup injeksi di dalam sumur telah teridentifikasi;Gbr.1.Beberapa sistem injeksi bekerja sesuai rencana, sementara yang lain gagal karena berbagai alasan.Beberapa pengembangan lapangan baru direncanakan untuk downhole chemical injection (DHCI);Namun;dalam beberapa kasus peralatan belum sepenuhnya memenuhi syarat.
Penerapan DHCI adalah tugas yang kompleks.Ini melibatkan penyelesaian dan desain sumur, kimia sumur, sistem topside dan sistem dosis kimia dari proses topside.Bahan kimia tersebut akan dipompa dari sisi atas melalui jalur injeksi kimia ke peralatan penyelesaian dan turun ke dalam sumur.Oleh karena itu, dalam perencanaan dan pelaksanaan jenis proyek kerjasama antara beberapa disiplin sangat penting.Berbagai pertimbangan harus dievaluasi dan komunikasi yang baik selama desain itu penting.Insinyur proses, insinyur bawah laut, dan insinyur penyelesaian terlibat, berurusan dengan topik kimia sumur, pemilihan material, jaminan aliran, dan manajemen bahan kimia produksi.Tantangannya dapat berupa raja senjata kimia atau stabilitas suhu, korosi dan dalam beberapa kasus efek vakum karena tekanan lokal dan efek aliran di jalur injeksi kimia.Selain itu, kondisi seperti tekanan tinggi, suhu tinggi, laju gas tinggi, potensi penskalaan tinggi,pusar jarak jauh dan titik injeksi yang dalam di dalam sumur, memberikan tantangan dan persyaratan teknis yang berbeda untuk bahan kimia yang disuntikkan dan katup injeksi.
Tinjauan sistem DHCI yang dipasang di operasi Statoil menunjukkan bahwa pengalaman tersebut tidak selalu berhasil Tabel 1. Namun, perencanaan untuk peningkatan desain injeksi, kualifikasi bahan kimia, operasi dan pemeliharaan sedang dilakukan.Tantangannya bervariasi dari satu bidang ke bidang lain, dan masalahnya belum tentu katup injeksi kimia itu sendiri tidak berfungsi.
Selama beberapa tahun terakhir beberapa tantangan terkait jalur injeksi kimia downhole telah dialami.Dalam tulisan ini beberapa contoh diberikan dari pengalaman ini.Makalah ini membahas tantangan dan langkah-langkah yang diambil untuk memecahkan masalah terkait jalur DHCI.Dua sejarah kasus diberikan;satu di korosi dan satu di raja senjata kimia.Pengalaman lapangan yang menunjukkan kompleksitas sistem injeksi kontinu downhole mengenai masalah presipitasi dan korosi dibahas.
Studi laboratorium dan penerapan metode baru untuk kualifikasi kimia juga dipertimbangkan;cara memompa bahan kimia, potensi penskalaan dan pencegahannya, aplikasi peralatan yang rumit dan bagaimana bahan kimia tersebut akan mempengaruhi sistem bagian atas saat bahan kimia diproduksi kembali.Kriteria penerimaan untuk aplikasi bahan kimia melibatkan masalah lingkungan, efisiensi, kapasitas penyimpanan bagian atas, laju pompa, apakah pompa yang ada dapat digunakan, dll. Rekomendasi teknis harus didasarkan pada kompatibilitas cairan dan bahan kimia, deteksi residu, kompatibilitas bahan, desain pusat bawah laut, sistem dosis bahan kimia dan bahan di sekitar garis-garis ini.Bahan kimia mungkin perlu dihambat hidrat untuk mencegah penyumbatan saluran injeksi dari invasi gas dan bahan kimia tidak boleh membeku selama transportasi dan penyimpanan.Dalam pedoman internal yang ada terdapat daftar bahan kimia yang dapat diterapkan pada setiap titik dalam sistem Sifat fisik seperti viskositas penting.Sistem injeksi mungkin menyiratkan jarak 3-50 km dari garis aliran bawah laut pusar dan 1-3 km ke dalam sumur.Oleh karena itu, stabilitas suhu juga penting.Evaluasi efek hilir, misalnya di kilang mungkin juga harus dipertimbangkan.
Sistem injeksi kimia downhole
Manfaat biaya
Injeksi downhole penghambat kerak secara terus-menerus untuk melindungi DHS Vor pipa produksi mungkin hemat biaya dibandingkan memeras sumur dengan penghambat kerak.Aplikasi ini mengurangi potensi kerusakan formasi dibandingkan dengan perlakuan pemerasan kerak, mengurangi potensi masalah proses setelah pemerasan kerak dan memberikan kemungkinan untuk mengontrol laju injeksi bahan kimia dari sistem injeksi sisi atas.Sistem injeksi juga dapat digunakan untuk menginjeksi bahan kimia lain secara terus-menerus ke bawah lubang dan dengan demikian dapat mengurangi tantangan lain yang mungkin terjadi lebih jauh di hilir pabrik proses.
Sebuah studi komprehensif telah dilakukan untuk mengembangkan strategi skala downhole dari lapangan atau Oseberg S.Perhatian skala utama adalah CaCO;penskalaan di pipa atas dan kemungkinan kegagalan DHSV.Pertimbangan strategi manajemen skala atau Oseberg S menyimpulkan bahwa selama periode tiga tahun, DHCI adalah solusi yang paling hemat biaya di sumur tempat jalur injeksi kimia berfungsi.Elemen biaya utama sehubungan dengan teknik pemerasan skala yang bersaing adalah minyak yang ditangguhkan daripada biaya bahan kimia / operasional.Untuk penerapan scale inhibitor dalam gas lift, faktor utama pada biaya bahan kimia adalah laju angkat gas yang tinggi yang menyebabkan konsentrasi SI tinggi, karena konsentrasi harus diimbangi dengan laju angkat gas untuk menghindari raja senjata kimia.Untuk dua sumur di Oseberg S atau yang memiliki jalur DHC I yang berfungsi dengan baik, opsi ini dipilih untuk melindungi DHS V dari CaCO;penskalaan.
Sistem dan katup injeksi kontinu
Solusi penyelesaian yang ada menggunakan sistem injeksi kimia terus menerus menghadapi tantangan untuk mencegah penyumbatan saluran kapiler.Biasanya sistem injeksi terdiri dari saluran kapiler, diameter luar (OD) 1/4” atau 3/8”, dihubungkan ke manifold permukaan, diumpankan melalui-dan dihubungkan ke gantungan pipa di sisi annular pipa.Garis kapiler melekat pada diameter luar tabung produksi dengan klem kerah tabung khusus dan berjalan di bagian luar tabung sampai ke mandrel injeksi kimia.Mandrel secara tradisional ditempatkan di hulu DHS V atau lebih dalam di dalam sumur dengan maksud memberikan waktu dispersi yang cukup bagi bahan kimia yang disuntikkan dan untuk menempatkan bahan kimia di tempat tantangan ditemukan.
Pada katup injeksi kimia, Gbr.2, sebuah kartrid kecil berdiameter sekitar 1,5” berisi katup periksa yang mencegah cairan lubang sumur memasuki saluran kapiler.Itu hanyalah boneka kecil yang menunggangi pegas.Gaya pegas mengatur dan memprediksi tekanan yang diperlukan untuk membuka si kecil dari dudukan penyegelan.Saat bahan kimia mulai mengalir, si kecil diangkat dari dudukannya dan membuka katup periksa.
Diperlukan untuk memasang dua katup periksa.Satu katup adalah penghalang utama yang mencegah cairan lubang sumur memasuki saluran kapiler.Ini memiliki tekanan pembukaan yang relatif rendah (2-15bars). Jika tekanan hidrostatik di dalam garis kapiler kurang dari tekanan lubang sumur, cairan lubang sumur akan mencoba masuk ke dalam garis kapiler.Katup periksa lainnya memiliki tekanan bukaan atipikal 130-250 bar dan dikenal sebagai sistem pencegahan tabung-U.Katup ini mencegah bahan kimia di dalam saluran kapiler mengalir bebas ke lubang sumur jika tekanan hidrostatik di dalam saluran kapiler lebih besar daripada tekanan lubang sumur pada titik injeksi bahan kimia di dalam tabung produksi.
Selain dua katup periksa, biasanya ada filter in-line, tujuannya adalah untuk memastikan bahwa tidak ada serpihan apa pun yang dapat membahayakan kemampuan penyegelan sistem katup periksa.
Ukuran katup periksa yang dijelaskan agak kecil, dan kebersihan cairan yang disuntikkan sangat penting untuk fungsi operasionalnya.Dipercayai bahwa kotoran dalam sistem dapat dibuang dengan meningkatkan laju aliran di dalam saluran kapiler, sehingga katup periksa akan terbuka dengan sengaja.
Ketika katup periksa terbuka, tekanan yang mengalir dengan cepat menurun dan menyebar ke atas garis kapiler sampai tekanan kembali meningkat.Katup periksa kemudian akan menutup sampai aliran bahan kimia menghasilkan tekanan yang cukup untuk membuka katup;hasilnya adalah osilasi tekanan dalam sistem katup periksa.Semakin tinggi tekanan bukaan yang dimiliki sistem check valve, semakin sedikit area aliran yang terbentuk saat check valve terbuka dan sistem mencoba mencapai kondisi kesetimbangan.
Katup injeksi kimia memiliki tekanan bukaan yang relatif rendah;dan jika tekanan tabung pada titik masuk bahan kimia menjadi kurang dari jumlah tekanan hidrostatik bahan kimia di dalam saluran kapiler ditambah tekanan bukaan katup periksa, hampir vakum atau vakum akan terjadi di bagian atas saluran kapiler.Ketika injeksi bahan kimia berhenti atau aliran bahan kimia rendah, kondisi hampir vakum akan mulai terjadi di bagian atas garis kapiler.
Tingkat vakum tergantung pada tekanan lubang sumur, berat jenis campuran bahan kimia yang disuntikkan yang digunakan di dalam saluran kapiler, tekanan pembukaan katup periksa pada titik injeksi dan laju alir bahan kimia di dalam saluran kapiler.Kondisi sumur akan bervariasi selama umur lapangan dan potensi vakum karena itu juga akan bervariasi dari waktu ke waktu.Penting untuk menyadari situasi ini untuk mengambil pertimbangan dan tindakan pencegahan yang tepat sebelum tantangan yang diharapkan terjadi.
Bersama dengan tingkat injeksi yang rendah, biasanya pelarut yang digunakan dalam jenis aplikasi ini menguap menyebabkan efek yang belum sepenuhnya dieksplorasi.Efek ini adalah raja senjata atau presipitasi padatan, misalnya polimer, saat pelarut menguap.
Selanjutnya, sel galvanik dapat dibentuk dalam fase transisi antara permukaan fluida kimia dan fase gas hampir vakum yang diisi uap di atas.Hal ini dapat menyebabkan korosi lubang lokal di dalam garis kapiler sebagai akibat dari peningkatan agresivitas bahan kimia dalam kondisi ini.Serpihan atau kristal garam yang terbentuk sebagai film di dalam garis kapiler saat bagian dalamnya mengering dapat menyumbat atau menyumbat garis kapiler.
Nah filosofi penghalang
Saat merancang solusi sumur yang kuat, Statoil mensyaratkan bahwa keamanan sumur tersedia setiap saat selama siklus hidup sumur.Jadi, Statoil mensyaratkan bahwa ada dua pembatas sumur independen yang utuh.Gambar 3 menunjukkan skema penghalang sumur atipikal, di mana warna biru mewakili selubung penghalang sumur utama;dalam hal ini tabung produksi.Warna merah mewakili selubung penghalang sekunder;casing.Di sisi kiri sketsa injeksi kimia ditunjukkan sebagai garis hitam dengan titik injeksi ke pipa produksi di area bertanda merah (penghalang sekunder).Dengan memasukkan sistem injeksi bahan kimia ke dalam sumur, penghalang lubang sumur primer dan sekunder terancam bahaya.
Sejarah kasus korosi
Urutan kejadian
Injeksi kimia downhole dari scale inhibitor telah diterapkan ke dalam ladang minyak yang dioperasikan oleh Statoil di Landas Kontinen Norwegia.Dalam hal ini scale inhibitor yang diterapkan awalnya telah memenuhi syarat untuk aplikasi topside dan subsea.Pelengkapan sumur dilanjutkan dengan pemasangan DHCIpointat2446mMD, Gbr.3.Injeksi downhole dari topside scale inhibitor dimulai tanpa pengujian bahan kimia lebih lanjut.
Setelah satu tahun beroperasi, kebocoran pada sistem injeksi bahan kimia diamati dan investigasi dimulai.Kebocoran berdampak buruk pada penghalang sumur.Peristiwa serupa terjadi di beberapa sumur dan beberapa di antaranya harus ditutup saat penyelidikan sedang berlangsung.
Tubing produksi ditarik dan dipelajari secara detail.Serangan korosi terbatas pada satu sisi pipa, dan beberapa sambungan pipa sangat berkarat sehingga benar-benar ada lubang di dalamnya.Baja krom 3% setebal 8,5 mm telah hancur dalam waktu kurang dari 8 bulan.Korosi utama telah terjadi di bagian atas sumur, dari kepala sumur hingga sekitar 380m MD, dan sambungan tubing terkorosi terburuk ditemukan sekitar 350m MD.Di bawah kedalaman ini sedikit atau tidak ada korosi yang teramati, tetapi banyak kotoran ditemukan pada pipa OD.
Casing 9-5/8'' juga dipotong dan ditarik dan efek serupa diamati;dengan korosi di bagian atas sumur di satu sisi saja.Kebocoran yang disebabkan oleh pecahnya bagian casing yang melemah.
Bahan jalur injeksi kimia adalah Paduan 825.
Kualifikasi kimia
Sifat kimia dan pengujian korosi adalah fokus penting dalam kualifikasi penghambat kerak dan penghambat kerak yang sebenarnya telah memenuhi syarat dan digunakan dalam aplikasi topside dan bawah laut selama beberapa tahun.Alasan penerapan downhole kimia yang sebenarnya adalah memperbaiki sifat lingkungan dengan mengganti bahan kimia downhole yang ada. Namun, penghambat kerak hanya digunakan pada suhu ambien bagian atas dan dasar laut (4-20℃).Ketika disuntikkan ke dalam sumur, suhu bahan kimia tersebut bisa mencapai 90℃, tetapi tidak ada pengujian lebih lanjut yang dilakukan pada suhu ini.
Tes korosivitas awal telah dilakukan oleh pemasok bahan kimia dan hasilnya menunjukkan 2-4mm/tahun untuk baja karbon pada suhu tinggi.Selama fase ini keterlibatan minimal kompetensi teknis material dari operator.Tes baru kemudian dilakukan oleh operator yang menunjukkan bahwa penghambat kerak sangat korosif untuk bahan dalam pipa produksi dan selubung produksi, dengan laju korosi melebihi 70 mm/tahun.Bahan jalur injeksi kimia Paduan 825 belum diuji terhadap penghambat kerak sebelum injeksi.Suhu sumur dapat mencapai 90℃ dan pengujian yang memadai harus dilakukan dalam kondisi ini.
Investigasi juga mengungkapkan bahwa penghambat kerak sebagai larutan pekat telah melaporkan pH <3,0.Namun, pH belum diukur.Kemudian pH yang diukur menunjukkan nilai pH yang sangat rendah yaitu 0-1.Ini menggambarkan perlunya pengukuran dan pertimbangan material selain nilai pH yang diberikan.
Interpretasi hasil
Garis injeksi (Gbr.3) dibangun untuk memberikan tekanan hidrostatik dari penghambat skala yang melebihi tekanan di dalam sumur di titik injeksi.Inhibitor disuntikkan pada tekanan yang lebih tinggi daripada yang ada di lubang sumur.Hal ini menghasilkan efek tabung-U pada penutupan sumur.Katup akan selalu terbuka dengan tekanan yang lebih tinggi di saluran injeksi daripada di dalam sumur.Vakum atau penguapan di jalur injeksi dapat terjadi.Laju korosi dan risiko pitting paling besar di zona transisi gas/cair akibat penguapan pelarut.Eksperimen laboratorium yang dilakukan pada kupon mengkonfirmasi teori ini.Pada sumur yang mengalami kebocoran, semua lubang pada jalur injeksi terletak di bagian atas jalur injeksi kimia.
Gambar 4 menunjukkan fotografi garis DHC I dengan korosi pitting yang signifikan.Korosi yang terlihat pada pipa produksi bagian luar menunjukkan paparan lokal penghambat kerak dari titik kebocoran pitting.Kebocoran tersebut disebabkan oleh korosi sumuran oleh bahan kimia yang sangat korosif dan kebocoran melalui jalur injeksi bahan kimia ke dalam casing produksi.Penghambat kerak disemprotkan dari saluran kapiler berlubang ke casing dan pipa dan terjadi kebocoran.Konsekuensi sekunder dari kebocoran pada jalur injeksi belum dipertimbangkan.Disimpulkan bahwa korosi casing-dan tubing adalah hasil dari inhibitor kerak terkonsentrasi yang didoakan dari pipa kapiler berlubang ke casing dan tubing, Gbr.5.
Dalam hal ini ada kurangnya keterlibatan insinyur kompetensi material.Korosivitas bahan kimia pada jalur DHCI belum diuji dan efek sekunder akibat kebocoran belum dievaluasi;seperti apakah bahan di sekitarnya dapat mentolerir paparan bahan kimia.
Sejarah kasus raja senjata kimia
Urutan kejadian
Strategi pencegahan kerak untuk bidang HP HT adalah penyuntikan penghambat kerak secara terus-menerus di hulu katup pengaman lubang bawah.Potensi penskalaan kalsium karbonat yang parah diidentifikasi di dalam sumur.Salah satu tantangannya adalah suhu tinggi dan tingkat produksi gas dan kondensat yang tinggi dikombinasikan dengan tingkat produksi air yang rendah.Kekhawatiran dengan menyuntikkan penghambat kerak adalah bahwa pelarut akan terkelupas oleh laju produksi gas yang tinggi dan raja senjata kimia akan terjadi pada titik injeksi di hulu katup pengaman di dalam sumur, Gbr.1.
Selama kualifikasi penghambat kerak, fokusnya adalah pada efisiensi produk pada kondisi HP HT termasuk perilaku dalam sistem proses bagian atas (suhu rendah).Pengendapan penghambat kerak itu sendiri di dalam tabung produksi karena laju gas yang tinggi menjadi perhatian utama.Tes laboratorium menunjukkan bahwa penghambat kerak dapat mengendap dan melekat pada dinding tabung.Oleh karena itu, pengoperasian katup pengaman dapat mengalahkan risiko.
Pengalaman menunjukkan bahwa setelah beberapa minggu beroperasi, jalur kimia bocor.Dimungkinkan untuk memantau tekanan lubang sumur pada pengukur permukaan yang dipasang di saluran kapiler.Garis diisolasi untuk mendapatkan integritas yang baik.
Jalur injeksi kimia ditarik keluar dari sumur, dibuka dan diperiksa untuk mendiagnosis masalah dan menemukan kemungkinan penyebab kegagalan.Seperti dapat dilihat pada Gbr.6, sejumlah besar endapan ditemukan dan analisis kimia menunjukkan bahwa beberapa di antaranya adalah penghambat kerak.Endapan terletak di segel dan si kecil dan katup tidak dapat dioperasikan.
Kegagalan katup disebabkan oleh puing-puing di dalam sistem katup yang mencegah katup periksa memakan logam ke dudukan logam.Puing-puing diperiksa dan partikel utama terbukti serutan logam, mungkin dihasilkan selama proses pemasangan saluran kapiler.Selain itu, beberapa serpihan putih teridentifikasi pada kedua check valve terutama di bagian belakang katup.Ini adalah sisi tekanan rendah, yaitu sisi yang akan selalu bersinggungan dengan fluida lubang sumur.Awalnya, ini diyakini sebagai puing-puing dari lubang sumur produksi karena katup macet saat terbuka dan terkena cairan lubang sumur.Namun pemeriksaan puing-puing tersebut ternyata merupakan polimer dengan sifat kimia yang mirip dengan bahan kimia yang digunakan sebagai penghambat kerak.Ini menarik minat kami dan Statoil ingin mengeksplorasi alasan di balik puing-puing polimer yang ada di garis kapiler.
Kualifikasi kimia
Di bidang HP HT terdapat banyak tantangan sehubungan dengan pemilihan bahan kimia yang sesuai untuk mengurangi berbagai masalah produksi.Dalam kualifikasi scale inhibitor untuk downhole injeksi kontinu, pengujian berikut dilakukan:
● Stabilitas produk
● Penuaan termal
● Uji kinerja dinamis
● Kompatibilitas dengan air formasi dan inhibitor hidrat (MEG)
● Tes raja senjata statis dan dinamis
● Air informasi pembubaran ulang, bahan kimia segar dan MEG
Bahan kimia akan disuntikkan pada tingkat dosis yang telah ditentukan,tetapi produksi air belum tentu konstan,yaitu slugging air.Di antara siput air,ketika bahan kimia memasuki lubang sumur,itu akan bertemu dengan panas,aliran cepat gas hidrokarbon.Ini mirip dengan menyuntikkan penghambat kerak dalam aplikasi pengangkat gas (Fleming etal.2003). Bersama dengan
temperatur gas yang tinggi,risiko pengupasan pelarut sangat tinggi dan raja senjata dapat menyebabkan penyumbatan katup injeksi.Ini adalah risiko bahkan untuk bahan kimia yang diformulasikan dengan pelarut dengan titik didih tinggi/tekanan uap rendah dan Depresan Tekanan Uap lainnya (VPD's). Jika terjadi penyumbatan sebagian,aliran air formasi,MEG dan/atau bahan kimia segar harus dapat menghilangkan atau melarutkan kembali bahan kimia yang didehidrasi atau dibuang.
Dalam hal ini rig uji laboratorium baru dirancang untuk mereplikasi kondisi aliran di dekat lubang injeksi pada HP/HTg sebagai sistem produksi.Hasil dari uji raja senjata dinamis menunjukkan bahwa di bawah kondisi aplikasi yang diusulkan, kehilangan pelarut yang signifikan tercatat.Hal ini dapat menyebabkan raja senjata yang cepat dan akhirnya memblokir jalur aliran.Oleh karena itu, pekerjaan menunjukkan bahwa ada risiko yang relatif signifikan untuk injeksi bahan kimia terus menerus di sumur-sumur ini sebelum produksi air dan mengarah pada keputusan untuk menyesuaikan prosedur permulaan normal untuk bidang ini, menunda injeksi bahan kimia hingga terobosan air terdeteksi.
Kualifikasi scale inhibitor untuk continuous injection downhole memiliki fokus tinggi pada pengupasan pelarut dan gun king dari scale inhibitor pada titik injeksi dan di flowline tetapi potensi gun king di injection valve itu sendiri tidak dievaluasi.Katup injeksi mungkin gagal karena kehilangan pelarut yang signifikan dan raja senjata cepat,Gbr.6.Hasil menunjukkan bahwa penting untuk memiliki pandangan holistik dari sistem;tidak hanya fokus pada tantangan produksi,tetapi juga tantangan terkait injeksi bahan kimia,yaitu katup injeksi.
Pengalaman dari bidang lain
Salah satu laporan awal tentang masalah dengan jalur injeksi kimia jarak jauh adalah dari bidang satelit Gull fak sandVig dis (Osa etal.2001). Jalur injeksi bawah laut diblokir dari pembentukan hidrat di dalam jalur karena invasi gas dari cairan yang dihasilkan. ke saluran melalui katup injeksi.Pedoman baru untuk pengembangan bahan kimia produksi bawah laut dikembangkan.Persyaratan termasuk penghilangan partikel (filtrasi) dan penambahan inhibitor hidrat (misalnya glikol) ke semua inhibitor skala berbasis air untuk disuntikkan pada template bawah laut.Stabilitas kimia,viskositas dan kompatibilitas (cair dan bahan) juga dipertimbangkan.Persyaratan ini telah dimasukkan lebih jauh ke dalam sistem Statoil dan mencakup injeksi bahan kimia downhole.
Selama fase pengembangan Oseberg S atau lapangan, diputuskan bahwa semua sumur harus dilengkapi dengan sistem DHC I (Fleming et al.2006). Tujuannya adalah untuk mencegah CaCO;penskalaan di pipa atas dengan injeksi SI.Salah satu tantangan utama sehubungan dengan jalur injeksi kimia mencapai komunikasi antara permukaan dan outlet downhole.Diameter internal jalur injeksi kimia menyempit dari 7 mm menjadi 0,7 mm (ID) di sekitar katup pengaman annulus karena keterbatasan ruang dan kemampuan cairan untuk diangkut melalui bagian ini memengaruhi tingkat keberhasilan.Beberapa sumur platform memiliki saluran injeksi kimia yang terpasang,tetapi alasannya tidak dipahami.Kereta berbagai cairan (glikol,mentah,kondensat,xilena,penghambat skala,air dll.) diuji laboratorium untuk viskositas dan kompatibilitas dan dipompa maju dan mundur untuk membuka saluran;Namun,penghambat skala target tidak dapat dipompa sampai ke katup injeksi kimia.Lebih jauh,komplikasi terlihat dengan pengendapan penghambat kerak fosfonat bersama dengan sisa air garam penyelesaian CaClz dalam satu sumur dan raja senjata penghambat kerak di dalam sumur dengan rasio gasoil yang tinggi dan pemotongan air yang rendah (Fleming et al.2006)
Pelajaran yang dipelajari
Pengembangan metode pengujian
Pelajaran utama yang dipetik dari kegagalan sistem DHC I adalah sehubungan dengan efisiensi teknis penghambat kerak dan bukan sehubungan dengan fungsionalitas dan injeksi bahan kimia.Topside injection dan subsea injection telah berfungsi dengan baik dari waktu ke waktu;Namun,aplikasi telah diperluas ke injeksi kimia lubang bawah tanpa pembaruan yang sesuai dari metode kualifikasi kimia.Pengalaman Statoil dari dua kasus lapangan yang disajikan adalah bahwa dokumentasi yang mengatur atau pedoman kualifikasi bahan kimia harus diperbarui untuk memasukkan jenis aplikasi bahan kimia ini.Dua tantangan utama telah diidentifikasi sebagai i) vakum di jalur injeksi kimia dan ii) potensi pengendapan bahan kimia.
Penguapan bahan kimia dapat terjadi pada tabung produksi (seperti yang terlihat dalam kasus raja senjata) dan dalam tabung injeksi (antarmuka transien telah diidentifikasi dalam kasus vakum) ada risiko bahwa endapan ini dapat dipindahkan bersama aliran dan ke dalam katup injeksi dan selanjutnya ke dalam sumur.Katup injeksi sering dirancang dengan filter di hulu titik injeksi,ini tantangan,seperti dalam kasus pengendapan, filter ini mungkin tersumbat menyebabkan katup gagal.
Pengamatan dan kesimpulan awal dari pelajaran yang dipetik menghasilkan studi laboratorium yang ekstensif tentang fenomena tersebut.Tujuan keseluruhannya adalah untuk mengembangkan metode kualifikasi baru untuk menghindari masalah serupa di masa mendatang.Dalam penelitian ini berbagai pengujian telah dilakukan dan beberapa metode laboratorium telah dirancang (dikembangkan untuk) memeriksa bahan kimia sehubungan dengan tantangan yang teridentifikasi.
● Saring penyumbatan dan stabilitas produk dalam sistem tertutup.
● Pengaruh kehilangan sebagian pelarut pada korosivitas bahan kimia.
● Pengaruh hilangnya sebagian pelarut di dalam kapiler pada pembentukan padatan atau sumbat kental.
Selama pengujian metode laboratorium, beberapa masalah potensial telah diidentifikasi
● Penyumbatan filter berulang dan stabilitas yang buruk.
● Pembentukan padatan mengikuti penguapan parsial dari kapiler
● Perubahan PH karena hilangnya pelarut.
Sifat pengujian yang dilakukan juga telah memberikan informasi dan pengetahuan tambahan yang berkaitan dengan perubahan sifat fisik bahan kimia di dalam kapiler ketika mengalami kondisi tertentu.,dan bagaimana ini berbeda dari solusi massal yang mengalami kondisi serupa.Pekerjaan uji juga telah mengidentifikasi perbedaan yang cukup besar antara cairan curah,fase uap dan cairan residu yang dapat menyebabkan peningkatan potensi presipitasi dan/atau peningkatan korosifitas.
Prosedur uji korosifitas penghambat kerak dikembangkan dan disertakan dalam dokumentasi yang mengatur.Untuk setiap aplikasi pengujian korosivitas yang diperpanjang harus dilakukan sebelum injeksi inhibitor skala dapat diterapkan.Tes raja senjata dari bahan kimia di jalur injeksi juga telah dilakukan.
Sebelum memulai kualifikasi bahan kimia, penting untuk membuat ruang lingkup pekerjaan yang menggambarkan tantangan dan tujuan bahan kimia tersebut.Pada tahap awal, penting untuk mengidentifikasi tantangan utama agar dapat memilih jenis bahan kimia yang akan menyelesaikan masalah.Ringkasan kriteria penerimaan yang paling penting dapat ditemukan pada Tabel 2.
Kualifikasi bahan kimia
Kualifikasi bahan kimia terdiri dari pengujian dan evaluasi teoritis untuk setiap aplikasi.Spesifikasi teknis dan kriteria pengujian harus ditetapkan dan ditetapkan,misalnya dalam HSE,kecocokan bahan,stabilitas produk dan kualitas produk (partikel).Lebih jauh,titik beku,viskositas dan kompatibilitas dengan bahan kimia lainnya,penghambat hidrat,air formasi dan fluida yang dihasilkan harus ditentukan.Daftar metode uji yang disederhanakan yang mungkin digunakan untuk kualifikasi bahan kimia diberikan pada Tabel 2.
Fokus berkelanjutan dan pemantauan efisiensi teknis,tingkat dosis dan fakta HSE penting.Persyaratan suatu produk dapat mengubah umur lapangan atau pabrik proses;bervariasi dengan tingkat produksi serta komposisi cairan.Kegiatan tindak lanjut dengan evaluasi kinerja,optimalisasi dan/atau pengujian bahan kimia baru harus sering dilakukan untuk memastikan program perawatan yang optimal.
Tergantung kualitas minyaknya,produksi air dan tantangan teknis di pabrik produksi lepas pantai,penggunaan bahan kimia produksi mungkin diperlukan untuk mencapai kualitas ekspor,persyaratan peraturan,dan untuk mengoperasikan instalasi lepas pantai dengan cara yang aman.Semua bidang memiliki tantangan yang berbeda, dan bahan kimia produksi yang dibutuhkan akan bervariasi dari satu bidang ke bidang lainnya dan dari waktu ke waktu.
Penting untuk fokus pada efisiensi teknis bahan kimia produksi dalam program kualifikasi,tetapi juga sangat penting untuk fokus pada sifat-sifat bahan kimia tersebut,seperti stabilitas,kualitas produk dan kompatibilitas.Kompatibilitas dalam pengaturan ini berarti kompatibilitas dengan cairan,bahan dan bahan kimia produksi lainnya.Ini bisa menjadi tantangan.Tidak disarankan untuk menggunakan bahan kimia untuk memecahkan masalah untuk kemudian menemukan bahwa bahan kimia tersebut berkontribusi atau menciptakan tantangan baru.Mungkin sifat kimia dan bukan tantangan teknis yang merupakan tantangan terbesar.
Persyaratan khusus
Persyaratan khusus pada filtrasi produk yang dipasok harus diterapkan untuk sistem bawah laut dan untuk downhole injeksi kontinu.Saringan dan filter dalam sistem injeksi kimia harus disediakan berdasarkan spesifikasi pada peralatan hilir dari sistem injeksi bagian atas,pompa dan katup injeksi,ke katup injeksi downhole.Di mana injeksi bahan kimia terus menerus downhole diterapkan, spesifikasi dalam sistem injeksi kimia harus didasarkan pada spesifikasi dengan kekritisan tertinggi.Ini mungkin filter di downhole katup injeksi.
Tantangan injeksi
Sistem injeksi mungkin menyiratkan jarak 3-50 km dari garis aliran bawah laut pusar dan 1-3 km ke dalam sumur.Sifat fisik seperti viskositas dan kemampuan memompa bahan kimia itu penting.Jika viskositas pada suhu dasar laut terlalu tinggi akan menjadi tantangan untuk memompa bahan kimia melalui jalur injeksi kimia di pusar bawah laut dan ke titik injeksi bawah laut atau di dalam sumur.Viskositas harus sesuai dengan spesifikasi sistem pada suhu penyimpanan atau operasional yang diharapkan.Ini harus dievaluasi dalam setiap kasus,dan akan bergantung pada sistem.Seperti tabel laju injeksi kimia merupakan salah satu faktor keberhasilan dalam injeksi kimia.Untuk meminimalkan risiko penyumbatan jalur injeksi kimia,bahan kimia dalam sistem ini harus dihambat hidrat (jika berpotensi hidrat).Kompatibilitas dengan cairan yang ada dalam sistem (cairan pengawet) dan penghambat hidrat harus dilakukan.Uji stabilitas bahan kimia pada suhu sebenarnya (suhu lingkungan serendah mungkin,suhu sekitar,temperatur bawah laut,suhu injeksi) harus dilewati.
Program untuk mencuci saluran injeksi kimia pada frekuensi tertentu juga harus diperhatikan.Mungkin memberikan efek pencegahan untuk secara teratur menyiram jalur injeksi kimia dengan pelarut,glikol atau bahan kimia pembersih untuk menghilangkan kemungkinan endapan sebelum terakumulasi dan dapat menyebabkan penyumbatan saluran.Solusi kimia yang dipilih dari cairan pembilas haruskompatibel dengan bahan kimia di jalur injeksi.
Dalam beberapa kasus, jalur injeksi kimia digunakan untuk beberapa aplikasi kimia berdasarkan tantangan yang berbeda selama masa pakai lapangan dan kondisi fluida.Pada fase produksi awal sebelum terobosan air, tantangan utama dapat berbeda dari tantangan pada masa akhir yang sering dikaitkan dengan peningkatan produksi air.Untuk mengubah dari inhibitor berbasis pelarut non-air seperti inhibitor ene aspal ke kimia berbasis air seperti inhibitor skala dapat memberikan tantangan dengan kompatibilitas.Oleh karena itu penting untuk fokus pada kompatibilitas dan kualifikasi serta penggunaan spacer saat direncanakan untuk mengganti bahan kimia di jalur injeksi bahan kimia.
Bahan
Mengenai kompatibilitas bahan,semua bahan kimia harus kompatibel dengan segel,elastomer,gasket dan bahan konstruksi yang digunakan dalam sistem injeksi kimia dan pabrik produksi.Prosedur uji korosifitas bahan kimia (misalnya inhibitor kerak asam) untuk lubang injeksi kontinu harus dikembangkan.Untuk setiap aplikasi pengujian korosivitas yang diperpanjang harus dilakukan sebelum injeksi bahan kimia dapat diterapkan.
Diskusi
Keuntungan dan kerugian injeksi kimia downhole terus menerus harus dievaluasi.Injeksi penghambat kerak secara terus-menerus untuk melindungi DHS Vor pipa produksi adalah metode elegan untuk melindungi sumur dari kerak.Seperti disebutkan dalam makalah ini ada beberapa tantangan dengan injeksi kimia downhole terus menerus,namun untuk mengurangi risiko, penting untuk memahami fenomena yang terkait dengan solusi.
Salah satu cara untuk mengurangi risiko adalah dengan fokus pada pengembangan metode pengujian.Dibandingkan dengan topside atau subsea chemical injection ada kondisi yang berbeda dan lebih parah di dalam sumur.Prosedur kualifikasi untuk bahan kimia untuk injeksi terus menerus bahan kimia downhole harus mempertimbangkan perubahan kondisi ini.Kualifikasi bahan kimia harus dibuat sesuai dengan bahan yang mungkin bersentuhan dengan bahan kimia.Persyaratan untuk kualifikasi kompatibilitas dan pengujian pada kondisi yang mereplikasi sedekat mungkin dengan berbagai kondisi siklus hidup sumur yang akan digunakan sistem ini harus diperbarui dan diterapkan.Pengembangan metode pengujian harus dikembangkan lebih lanjut menjadi pengujian yang lebih realistis dan representatif.
Selain itu,interaksi antara bahan kimia dan peralatan sangat penting untuk sukses.Pengembangan katup injeksi kimia harus mempertimbangkan sifat kimia dan lokasi katup injeksi di dalam sumur.Harus dipertimbangkan untuk menyertakan katup injeksi nyata sebagai bagian dari peralatan pengujian dan untuk melakukan pengujian kinerja penghambat kerak dan desain katup sebagai bagian dari program kualifikasi.Untuk memenuhi syarat scale inhibitor,fokus utama sebelumnya adalah pada tantangan proses dan penghambatan skala,tetapi penghambatan skala yang baik tergantung pada injeksi yang stabil dan terus menerus.Tanpa injeksi yang stabil dan terus menerus, potensi skala akan meningkat.Jika katup injeksi penghambat kerak rusak dan tidak ada injeksi penghambat kerak ke dalam aliran fluida,sumur dan katup pengaman tidak terlindungi dari kerak dan karenanya produksi yang aman dapat terancam.Prosedur kualifikasi harus memperhatikan tantangan terkait injeksi penghambat kerak selain tantangan proses dan efisiensi penghambat kerak yang memenuhi syarat.
Pendekatan baru melibatkan beberapa disiplin dan kerjasama antara disiplin dan tanggung jawab masing-masing harus diperjelas.Dalam aplikasi ini sistem proses topside,templat bawah laut dan desain serta penyelesaian sumur terlibat.Jaringan multi-disiplin yang berfokus pada pengembangan solusi kuat untuk sistem injeksi kimia adalah penting dan mungkin merupakan jalan menuju sukses.Komunikasi antara berbagai disiplin ilmu sangat penting;komunikasi yang sangat erat antara ahli kimia yang memiliki kendali atas bahan kimia yang digunakan dan insinyur sumur yang memiliki kendali atas peralatan yang digunakan dalam sumur adalah penting.Untuk memahami tantangan disiplin ilmu yang berbeda dan belajar dari satu sama lain sangat penting untuk memahami kompleksitas dari keseluruhan proses.
Kesimpulan
● Injeksi penghambat kerak secara terus-menerus untuk melindungi DHS Vor pipa produksi adalah metode elegan untuk melindungi sumur dari kerak
● Untuk mengatasi tantangan yang teridentifikasi,rekomendasi berikut adalah:
● Prosedur kualifikasi DHCI khusus harus dilakukan.
● Metode kualifikasi untuk katup injeksi kimia
● Metode pengujian dan kualifikasi untuk fungsionalitas bahan kimia
● Pengembangan metode
● Pengujian material yang relevan
● Interaksi multidisiplin di mana komunikasi antara berbagai disiplin ilmu yang terlibat sangat penting untuk keberhasilan.
Terima kasih
Penulis ingin mengucapkan terima kasih kepada Statoil AS A untuk izin untuk menerbitkan karya ini dan Baker Hughes dan Schlumberger untuk mengizinkan penggunaan gambar di Fig.2.
Tata nama
(Ba/Sr)SO4=barium/strontium sulfat
CaCO3 = kalsium karbonat
DHCI = injeksi kimia bawah lubang
DHSV = katup pengaman lubang bawah
misalnya = misalnya
GOR = rasio bahan bakar minyak
HSE = lingkungan keselamatan kesehatan
HPHT = tekanan tinggi suhu tinggi
ID = diameter dalam
yaitu = itu
km = kilometer
mm=milimeter
MEG = mono etilen glikol
mMD = kedalaman terukur meter
OD = diameter luar
SI = penghambat skala
mTV D = meter total kedalaman vertikal
U-tube = tabung berbentuk U
VPD = penekan tekanan uap
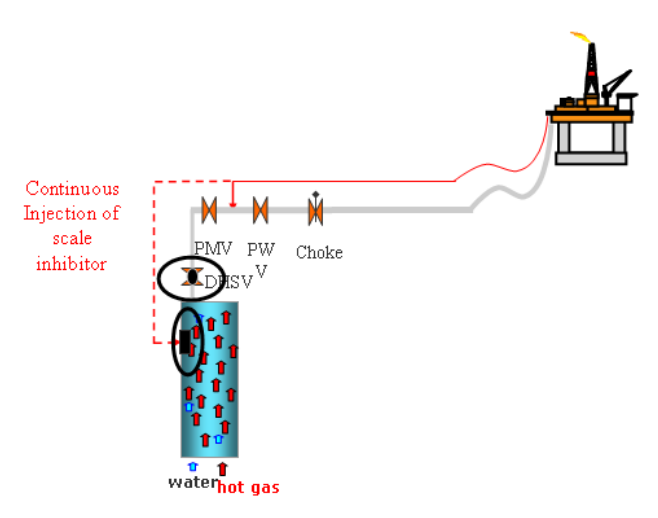
Gambar 1. Tinjauan sistem injeksi kimia bawah laut dan bawah lubang di lapangan yang tidak biasa.Sketsa injeksi kimia up stream DHSV dan tantangan terkait yang diharapkan.DHS V=katup pengaman downhole, PWV=katup sayap proses dan PM V=katup master proses.
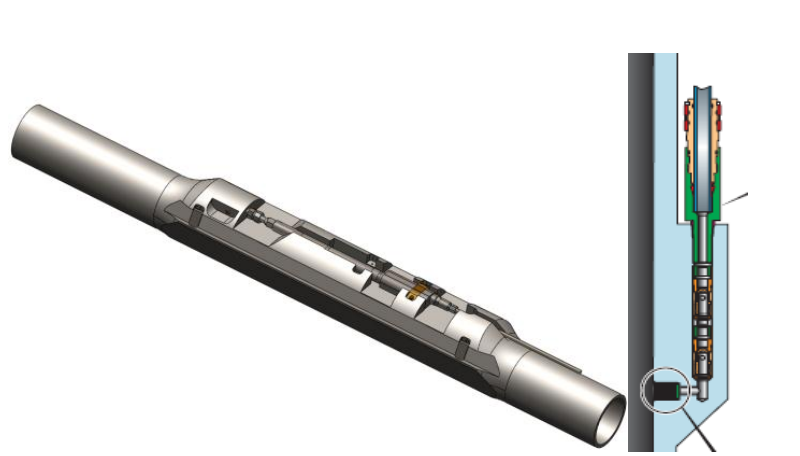
Gambar 2. Sketsa sistem injeksi kimia downhole atipikal dengan mandrel dan katup.Sistem dihubungkan ke manifold permukaan, diumpankan melalui-dan dihubungkan ke gantungan pipa di sisi annular pipa.Mandrel injeksi kimia secara tradisional ditempatkan jauh di dalam sumur dengan maksud untuk memberikan perlindungan kimia.
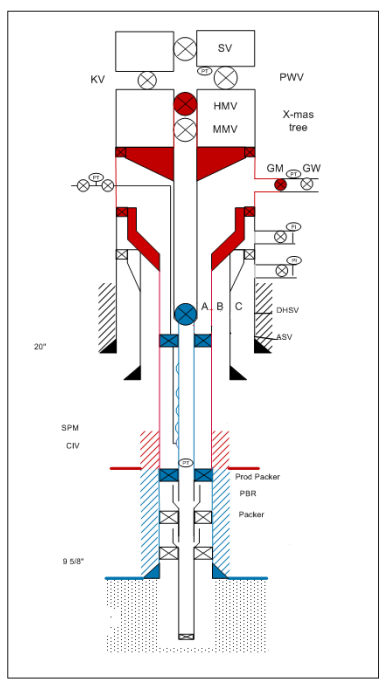
Gambar 3. Skema penghalang sumur tipikal,di mana warna biru mewakili selubung penghalang sumur utama;dalam hal ini tabung produksi.Warna merah mewakili selubung penghalang sekunder;casing.Di sisi kiri ditunjukkan injeksi kimia, garis hitam dengan titik injeksi ke pipa produksi di area bertanda merah (penghalang sekunder).
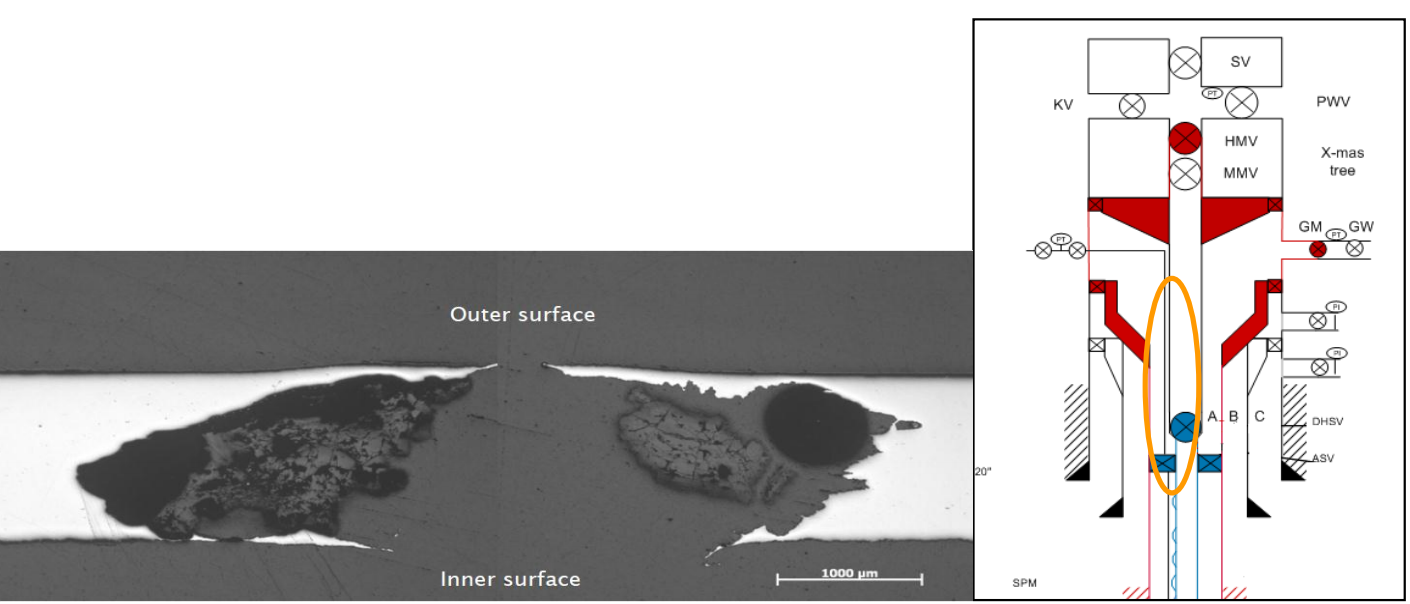
Gambar 4. Lubang berlubang ditemukan di bagian atas jalur injeksi 3/8”.Area tersebut ditunjukkan dalam sketsa skematik penghalang sumur atipikal, ditandai dengan elips jingga.
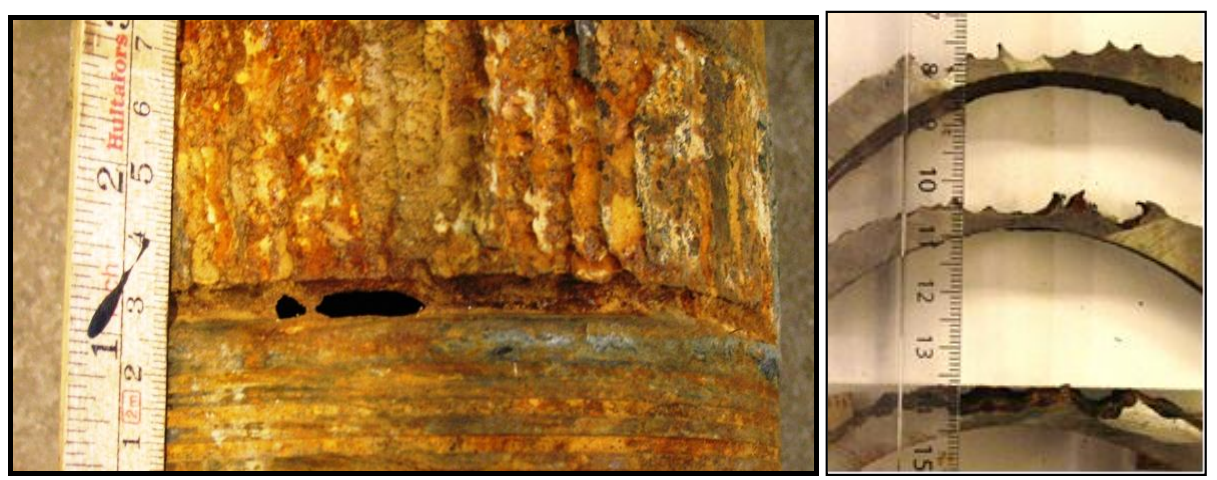
Gambar 5. Serangan korosi yang parah pada tabung Chrome 7” 3%.Gambar menunjukkan serangan korosi setelah penghambat kerak disemprotkan dari jalur injeksi kimia berlubang ke pipa produksi.
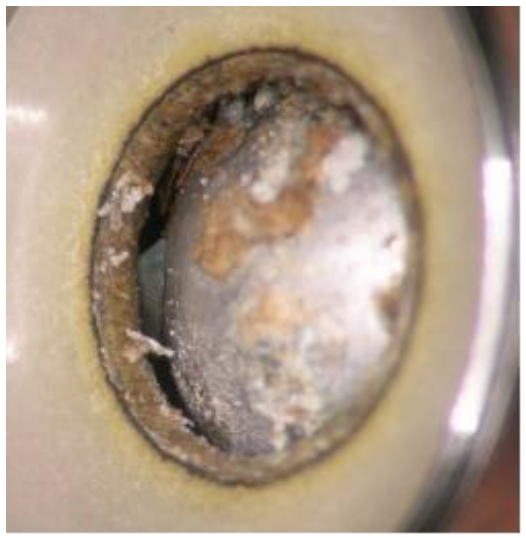
Gambar 6. Kotoran ditemukan di katup injeksi kimia.Puing-puing dalam hal ini adalah serutan logam yang mungkin berasal dari proses pemasangan selain beberapa kotoran keputihan.Pemeriksaan puing-puing putih terbukti merupakan polimer dengan kimia yang mirip dengan bahan kimia yang disuntikkan
Waktu posting: Apr-27-2022